The Benefits of Lean Manufacturing: Why and How to Go Lean
Posted on
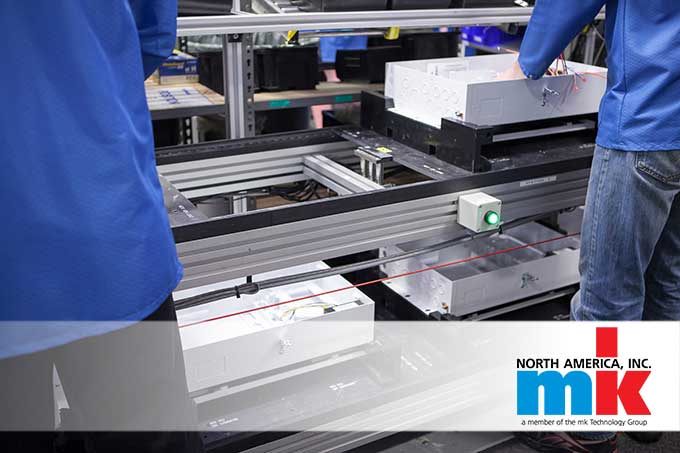
Efficiency has never been more important to the manufacturing industry than now. This is especially true in North America, where higher costs of doing business place many manufacturers at a competitive disadvantage with global counterparts in places like China, India, and Indonesia.
How can North American manufacturers maximize productivity and reduce waste enough to remain competitive in the global marketplace? For many, the answer is with a set of principles and practices collectively known as lean manufacturing.
What Is Lean Manufacturing?
Sometimes called “lean production,” lean manufacturing is a series of methods designed to minimize the waste of material and labor while maintaining or increasing levels of production. This results in a net improvement in total productivity.
Lean manufacturing’s roots lie in Japanese manufacturing with the Toyota Production System. Lean principles pioneered by Toyota include “just-in-time” manufacturing, where inventory is kept at low “as-needed” levels; automation supervised by human workers to maintain quality control (known as jidoka); minimization of downtime and transportation, and others.
Ultimately, lean manufacturing is about eliminating that which does not add value, and delivering the best possible product to the customer as quickly and with as few barriers as possible.
The Benefits of Lean Manufacturing
Lean manufacturing improves efficiency, reduces waste, and increases productivity. The benefits, therefore, are manifold:
- Increased product quality: Improved efficiency frees up employees and resources for innovation and quality control that would have previously been wasted.
- Improved lead times: As manufacturing processes are streamlined, businesses can better respond to fluctuations in demand and other market variables, resulting in fewer delays and better lead times.
- Sustainability: Less waste and better adaptability makes for a business that’s better equipped to thrive well into the future.
- Employee satisfaction: Workers know when their daily routine is bloated or packed with unnecessary work, and it negatively affects morale. Lean manufacturing boosts not only productivity, but employee satisfaction.
- Increased profits: And, of course, more productivity with less waste and better quality ultimately makes for a more profitable company.
Lean Manufacturing in Practice
To paraphrase the Anna Karenina principle, all efficient companies are alike; every inefficient company is inefficient in its own way.
Implementing lean manufacturing practices in part means identifying and eliminating the wasteful practices and procedures that are specific to your business, and replacing them with more optimized lean strategies.
Just a few examples of lean manufacturing in practice include:
- Value stream and process mapping: Value stream mapping and process mapping involve evaluating and charting broad and specific processes to better understand precise areas of waste. Once processes are mapped and analyzed, existing issues can be pinpointed and eliminated or streamlined.
- Tightly controlled automation and production flow: Well-implemented assembly lines are essential to lean production. Lines should be automated where possible, but accommodate live workers where quality control demands.
- Inventory reduction and Kanban: Under lean production practices, inventory levels are strictly regulated, often using a system called Kanban. With a Kanban system, essential inventory is replaced only when an employee takes a small “Kanban card” to a supervisor; inventory is then procured or replaced strictly as needed. Inventory is kept with corresponding Kanban cards on a centrally located Kanban rack.
- Employee training: Employees should be trained not only on lean principles, but on the specific lean methods and processes to be utilized moving forward.
How mk North America Can Help with Lean Production
While most of lean production is about process and philosophy, there is a great deal of physical infrastructure required to do it right. For that, mk North America can help.
mk North America is a leading extruded aluminum and conveyor manufacturer, offering numerous products that can help with lean manufacturing workflow and implementation.
Conveyor systems from mk North America are the industry standard for efficiency and flexibility, offering modular design and custom solutions that can’t be beat. Industrial workstations made with extruded aluminum can also be integrated and reintegrated along production lines to keep workers where they need to be with the right tools on-hand.
For inventory control, mk North America’s aluminum extrusions can be used to make custom Kanban racks, material shuttles, and more.
To learn more about how mk North America can help improve your company’s manufacturing efficiency, get in touch by calling (860) 769-5500 or using this online form.